About Us
What is Sheet Metal Fabrication?
If you’re new to sheet metal fabricating, sheet metal fabrication refers to multiple subtractive manufacturing processes that utilize thin metal sheets to produce parts. To begin, a sheet metal fabricator will convert a CAD design or engineering drawing into machine code. Then, a CO2 laser cutting, water jet cutting, wire EDM, or other sheet metal cutting machine will begin to remove material to form the geometries of the desired part. After the material is cut, the material is bent or formed into the correct shape. The part then moves to post-processing or assembly, including adding inserts, welding or finishing. Sheet metal parts, including chassis, brackets, enclosures and more, are favored by a wide range of industries for their durability and high precision. Applications include industrial, aerospace, defense, automotive, consumer products and more.
Sheet Metal Fabrication Processes
We offer several sheet metal fabrication processing including cutting, etching, punching and more.
Here are many of the processes and services offered:
Here are many of the processes and services offered:
Fiber Laser Cutting
Solid-state lasers, such as the fiber optic laser, use laser diodes transmitted through optical fibers to create the desired cuts. The laser cutting machine uses no mechanical components and makes its cuts within an enclosure. This means the operation produces less noise and decreases the personal risk of the operator. The fiber laser cutting process is highly efficient thanks to the cutter’s high-power output and high-intensity level.Waterjet Cutting
A water jet cutting machine is used to produce flat-cut parts. The waterjet is attached to a high-pressure pump which forces water through a nozzle to create precise cuts. The balance between velocity and volume is what facilitates the cut. When an abrasive water cut is needed, the abrasive substance is mixed with the water stream. The water and some abrasive substances used during the process can be recycled and reused, which reduces costs while increasing energy efficiency.Wire EDM
Wire EDM uses heat from electrical currents to cut through metal. EDM is a no-contact spark erosion process that reduces the need for secondary finishes. During EDM machining, a metal piece is submerged into de-ionized water (dielectric). An electrically charged thin metal wire (no thicker than hair) melts through the metal using heat from the electrical sparks. The wire does not make contact with the workpiece. The voltage allows the spark from the wire to jump the gap between the wire and the workpiece, and the material begins to melt. The wire holds one side of the charge, while the conductive material holds the other side. The liquid dielectric controls the electrical sparks, cools, and flushes away the cut material.Microcut™ Micro Water Jet Cutting
Micro jet water cutting is water jet manufacturing at a micro-level. Water jet cutting allows for the cutting of tiny, complex parts with great accuracy.Stamping
A blanked or coiled piece of sheet metal is loaded into a stamping press where a die (stamping tool) in the shape of the desired part is pressed down into the metal. Stamping includes punching, blanking, bending, drawing, embossing and more.Forming
The sheet metal material is placed onto a flatbed. Next, a laser cutter begins to draw pre-programmed parts onto the material. A sheet metal punch may be used to form additional features. After deburring, the part is moved to the press brake, where they are shaped further. The part then moves to the finishing stage.Prototype Etching
Prototype etching may involve photochemical machining, chemical milling or acid etching. Chemical etching is a subtractive sheet metal manufacturing process that selectively removes material using baths of temperature-controlled etching chemicals. Chemical etching has a short lead time and inexpensive tooling, making it ideal for prototyping.Production Etching
Photochemical machining or chemical etching produces highly precise metal parts with great intricacies. It is fast to produce, cost-efficient, offers greater design flexibility and eliminates the need for deburring, perfect for transitioning prototypes to production.Laser Cutting
Laser cutting is a manufacturing technique that utilizes a high-powered laser beam to cut, engrave or mark material. There are multiple types of laser cutting machines categorized by gas, liquid or solid-state. CO2 lasers are a gas state laser which use a carbon dioxide mixture to cut. Solid-state lasers, such as the fiber optic laser, use laser diodes transmitted through optical fibers to create the desired cuts.CNC Punching
Computer numerically-controlled punching involves a punch press machine that may have one head and tool rail design or multi-tool turret design. The machine moves the sheet metal in a 2-axis direction and positions the material under the punching ram. The punching ram punches a hole or form into the sheet metal.Hardware Installation
As part of our complete sheet metal fabricating program, we offer high-quality hardware installation services. Whether your project requires a low or high-volume production run, we can ensure efficiency.Welding / Spotwelding
We offer a variety of welding and spotwelding processes. Welding is used to join two metal surfaces together. Spotwelding uses copper alloy electrodes to direct the welding current to a “spot”, melting the material and effectively joining two pieces together.Sanding / Grinding
To achieve a perfect finish, we offer sanding and grinding services. Sanding is used to remove any scratches or burrs from a part after it has been laser cut or punched. Grinding is used to remove weld or to add any desired cosmetic surfaces.Liquid Painting
Liquid painting is a suitable alternative for projects where powder coating cannot be used. It can be formulated to have special corrosion-resistant properties while still offering a professional finish. If your project requires painted parts in custom colors, our facilities can meet your painting needs.Powder Coating
Powder coating involves finishing a sheet metal part using a paint applied as a powder, then cured, resulting in a high-quality finish. We offer matte, smooth, textured and a variety of other finishes.Screen Printing
A sheet metal part can be screen printed. Does your project require a custom graphic? We can add the design of your choice to your custom part in a variety of finishes and colors.Assembly & Kitting
We offer assembly and kitting in-house. Whether your part requires installing hardware using automated or manual processes, our experts will ensure your part is to your exact specifications to deliver a fully finished product.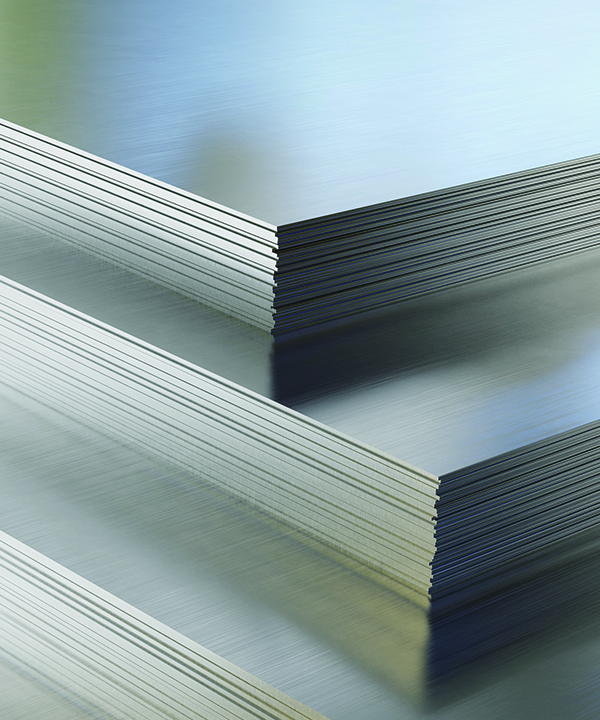
Common Sheet Metal Materials
We can help you match the right sheet metal material for your specific project. Some common materials for sheet metal fabrication include:
- Aluminum: Lightweight, great for lower temperatures, strong, corrosion-resistant, good heat conductivity, non-toxic
- Stainless Steel: Good strength and hardness ratio, durable, corrosion-resistant, very machinable
- Hot Rolled Steel: Good mechanical performance, good flexibility, lower cost
- Cold Rolled Steel: Good hardness and strength, good for tight tolerances, smooth surface and finish, high formability
- Brass: Lightweight, corrosion-resistant
- Copper: Corrosion-resistant, electrically conductive, ductile, and malleable
- Bronze: Low melting point and stronger than copper
- Magnesium: Low density, excellent stiffness
Sheet Metal Fabrication Processes
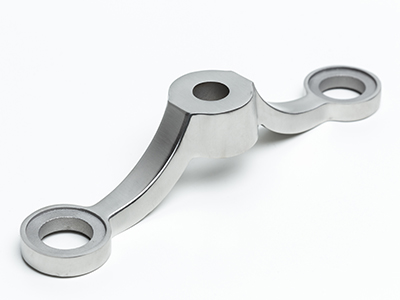
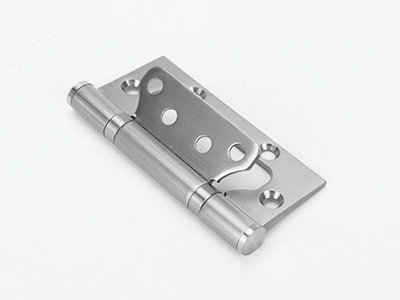
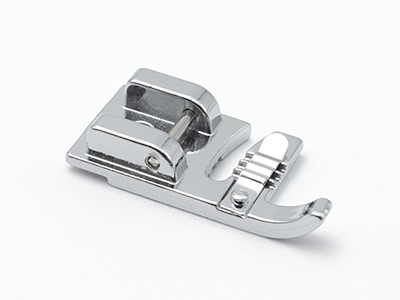
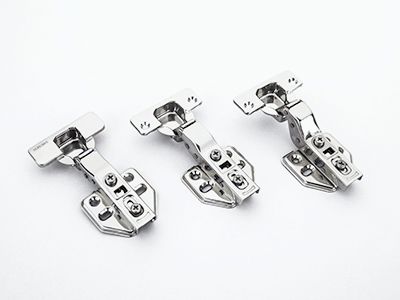
Designing Sheet Metal Parts: Best Practices
Gusset
- 1. Strengthens bends locally
- 2. Must be formed with custom tooling
- 3. Minimal tooling cost
- Whenever possible, maintain minimum spacing of 2-2.5x raw material thickness from edge of cutout to bend radius tangency.
- Lesser spacing requires secondary operations after bending and adds to manufacturing costs.
- Form angle and form radii should be made as large as possible.
- Offset should be minimized.
Rib
- 1. Stiffens flat sections
- 2. May require secondary trimming
- 3. Moderate tooling cost
- Close proximity form features can cause secondary operations after forming and adds to manufacturing cost.
- Form features in close proximity to each other increase forming strain which may cause “oil canning” or other deformation, fracturing or material separation.
Emboss
- 1. Adds strength
- 2. May be used for clearance
- 3. May be used as a standoff feature/dd>
- Form radii as large as possible to decrease forming strain. Separation may occur if form radii are too small.
- Raw material type and thickness impact feasibility.
- Create form angles larger than 90 degrees if possible.
- Minimize offset dimension.
- Form angle, offset dimension and overall shape of emboss are all factors that impact manufacturability.
Coin
- 1. Process by which metal currency is minted.
- 2. May be used for clearance
- 3. Requires moderately priced tooling./dd>
- Tooling cost depends on the size of coin features. Smaller features require more expensive tooling and forming processes.
- Significant material displacement may cause deformation of surrounding areas.
- Secondary operations may be required to trim displaced metal.
- Design for minimal material displacement.
Cut/Bend Relief
Design Tips:- To ensure cost-effective production, design cut and bend reliefs with a minimum of 2.5x material thickness.
- For prototype and short-run quantities, the minimum cut relief can be a laser or water jet cut kerf (0.010” – 0.040”).
- Lanced (sheared) features with zero cut relief are possible but require high-cost tooling.